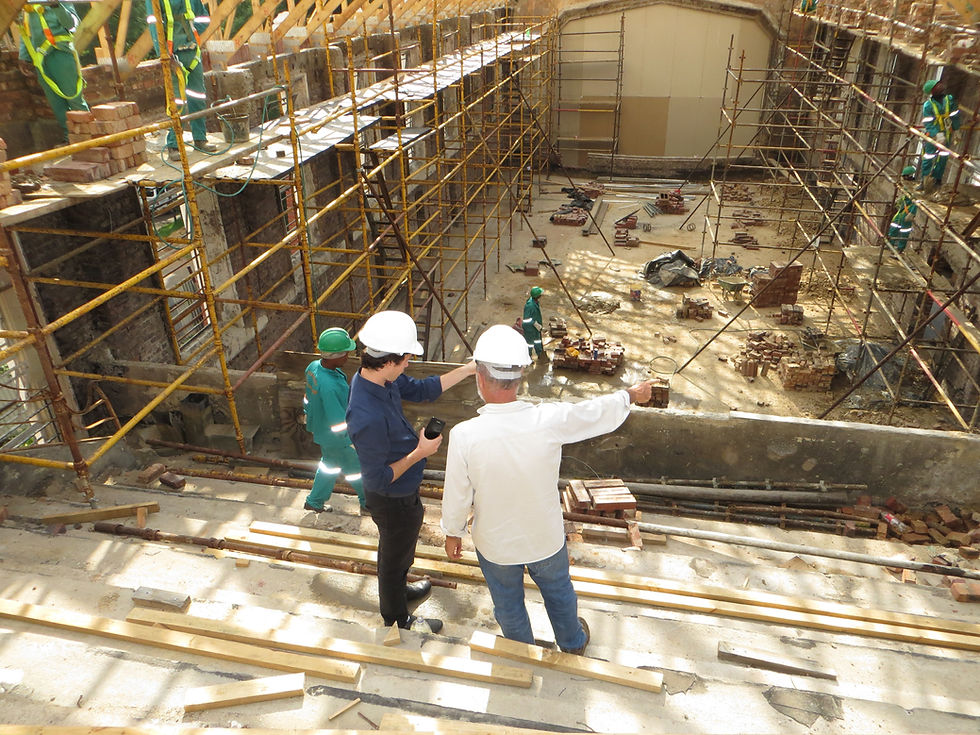
Price rises are expected amid the construction materials shortage which could impact your home project
The rate of increasing energy and raw material costs is the biggest concern facing the construction materials shortage, industry experts say.
The Construction Leadership Council (CLC) has warned that over the last three months inflation has increased by 10-15% on materials prices. This is likely to drive up the cost of materials and impact those working on self build, renovation and extension projects.
The cost of steel, cement, glass and other energy-intensive products are all expected to increase because of the energy crisis. And the increase in the price of raw materials in March was the highest in six months, which could constrain the availability of certain products.
Read on to learn which materials remain in short supply and which products could be expected to rise in price.
What's the Latest With the Construction Materials Shortage?
The construction materials shortage had blighted the construction throughout 2021, with a timber shortage and plaster shortage causing supply chain issues for those working on homebuilding and home improvement projects.
And just when the CLC confirmed in January that the industry was no longer experiencing extremely high levels of demand for building materials, and the shortage of HGV drivers was easing, surging energy price rises and the Ukraine war have started to reverse this progress.
In this month's S&P Global/CIPS construction Purchasing Managers' Index, a third of construction firms polled reported that delivery times for key materials are getting longer.
Energy prices
Average energy bills rose by 54% this month, which is putting pressure on construction firms due to energy intensive industries including concrete, steel and cement passing on the impact of higher prices.
"The volatility of energy prices has begun impacting the market. Some manufacturers of energy-intensive products are now warning of surcharges linked to energy costs," the CLC says.
Price inflation
Inflation is rising at its fastest rate for 30 years as fuel, energy and food costs surge. And the CLC reports that inflation concerns are leading some suppliers to only hold quotes for tender prices for 24 hours. The resulting uncertainty is reportedly leading some contractors to pause before entering fixed-price or long-term contracts.
"Without price continuity, it is harder for trades to quote for projects on fixed price contracts, and then seek to pass onto their customers any price increases for materials that would otherwise erode their profit margin," says the CLC.
Ukraine conflict
Industry groups and contractors are warning that Russia's invasion of Ukraine will lead to significant disruption to supply chains, which could lead to price hikes for a number of building materials. "The impact of the war in Ukraine is only beginning to be felt by UK construction," the CLC says.
Joe Sullivan, partner at MHA, adds: “Sector confidence has been boosted by some easing of supply chain issues so far this year, however the ongoing war in Ukraine is expected to put this in jeopardy. The true impact of the war and resulting sanctions on Russia will take time to materialise and as such, certain supply chains must swiftly pivot towards other sources for their materials."
Which Materials are Affected?
Supply challenges continued to affect a number of materials, including bricks, roof tiles, steel lintels and certain sealants, coatings and paints.
Bricks and blocks
There are ongoing challenges with bricks and blocks supply, the CLC says. Stocks increased slightly during the quieter winter months but as the market accelerates in the spring it will be essential for self builders to plan ahead and work with manufacturers to ensure timelines of availability.
Steel
At the start of the year Russia and Ukraine together constituted the second largest steel exporter in the world, and shortages on the continent are having a knock-on effect on the UK market. The biggest problem facing steel is cost, however, rather than availability.
Roof tiles
Long lead times remain for both concrete and clay roof tiles, averaging around 20-24 weeks, but can be up to 36 weeks for some products, according to the National Federation of Roofing Contractors (NFRC).
Paints and coatings
Paints and coatings remain affected by the ongoing raw material shortages, which has recently been exacerbated by further lockdowns in China and by the war in Ukraine. This could possibly affect the availability of some products over the coming months, the CLC says.
Electrical products
Some electrical products, particularly those using semi-conductors and microchips, could be subject to longer lead times.
Timber
The war in Ukraine and the resulting sanctions on Russia and Belarus are likely to constrain the supply of pallets, birch plywood and OSB (oriented strand board).
There could also be future supply issues with:
Plastic products
Ceramic tiles and sanitaryware
Aluminium
Copper
Lighting and fire protection systems
Kitchen white goods
Concrete
Insulation
Green Home Improvement Struggles
High prices and long delays are reportedly also affecting homeowners looking to go green and install energy-saving materials (ESMs) such as heat pumps and solar panels.
Demand is expected to rise for ESMs following the cut on VAT on retrofit measures announced in the Spring Statement, and following the launch of the Boiler Upgrade Scheme this month.
Moreover, the boiler market has been impacted by unprecedented demand coupled with supply chain challenges for steel, cardboard, plastics and electronic components, the CLC says.
When Will Building Materials Prices Stop Rising?
Prices have increased over the past 16 months for several materials, due to lengthening lead times and growing demand. This has made it difficult for manufacturers and suppliers to build up stock levels.
In a December Homebuilding & Renovating poll, 96% of respondents said "yes" when asked if they'd struggled to afford the cost of materials in 2021.
And year-on-year prices for all building work rose by 21.0% from February 2021 to February 2022, according to the BEIS Monthly Statistics of Building Materials and Components report for March.
British Steel announced a 25% on some products in March and has blamed the impact of of increasing energy, transport and raw materials costs. Meanwhile clay tiles have been subject to price increases due to rising energy costs, and Forterra has increased its brick prices.
These are some of the materials which continue to be affected:
Materials Price Tracker
Roof tiles - Prices have risen 24% in a year, according to price comparison service Quotation Check
Steel - Fabricated structural steel prices jumped 51% between February 2021 and February 2022 (BEIS)
Bricks - Brickmaker Forterra increased its brick prices by 12% from 1 April
Cement - The EY Item Club has warned that cement prices will keep rising in the coming months
Timber - The CLC says there have been marked increases in the price of MDF (medium density fibreboard)
How to Navigate Shortages
If you’re planning or in the middle of building work, then planning as far as you can in advance is pivotal to ensure you aren’t caught out by shortages or price rises.
The CLC advises self builders to work closely with their supply chain and communicate your requirements early with suppliers, distributors and builders merchants.
And Brian Berry from the Federation of Master Builders (FMB) says: “Product availability is proving to be a significant and prolonged issue for Britain’s builders, and consumers need to be aware that the cost of their building projects may change in the months ahead because of this pressure.
“However, I would caution against homeowners compromising quality and customer service, and defaulting to hire the builder with the cheapest quote.”
You can also use services such as Environmate to discover free and cheap building materials for your project. For more info about this article click here.
Comments